Tips & Strategies to Promote Health & Safety at workplace
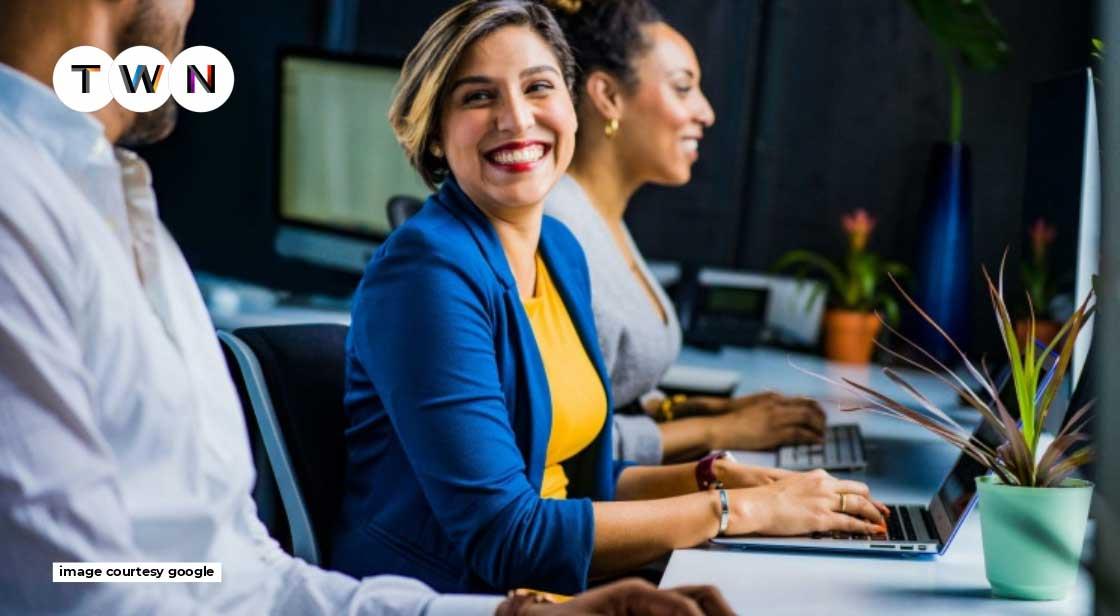
Blog Post
A person will love to work in a place where he can feel safe. Getting caught in an accident in the workplace is the worst nightmare of any working professional. To avoid that, zero-harm strategies came into existence. But what is it? Why is it important? We will talk about it in this blog post and tell you some ways to improve your workplace for your workers. On the World Day of Safety and Health at Work, we want you to know about a zero-harm workplace. Let’s learn about it. #TWN
Manager, “We are implementing a zero-harm culture in this organization after looking at some previous incidents.”
Employees, “What is that?”
Manager, “It is a way of safeguarding the employees in this workplace.”
Employees, “Oh, Okay.”
Sadly, very less people know about this zero-harm culture that has been around for a while now. Today, we celebrate World Day for Safety and Health at Work and try to aware people of this amazing culture.
Zero harm is a new safety culture movement that focuses on providing a perfectly safe environment for workers, contractors, and guests on a daily basis.
Despite the fact that zero harm culture has been widely criticized as being impossible to attain and unrealistic to expect, the new approach is gaining traction. Here's everything you need to know about zero harm culture and how certain strategies make this culture a useful one.
What Risk Management or Zero Harm Culture?
The term "zero harm" describes an approach to occupational health and safety that many workplaces have adopted. The primary objective of a zero-harm strategy is to conduct business in a workplace without subjecting employees to injury by implementing safe work systems. Approaches to zero-harm are associated with exceeding safety regulations.
The effectiveness of the zero-harm safety policy is debatable, with both practicing occupational health and safety experts and academic researchers debating it. Many safety experts support the concept, while others believe it is harmful. Because the zero-harm concept is not standardized and lacks a codified set of safety policies, processes, or review metrics, workplaces that use it may do so in a variety of ways.
Because of the emphasis on eliminating or reducing safety risks as a means of increasing workplace productivity, some work management methodologies have been framed as compatible with the zero-harm concept.
Adopting a zero-harm culture does not imply that you believe naively that all risks and hazards in your workplace will vanish and you will never have an accident again, as some critics of the movement appear to believe. Just as pursuing "inbox zero" (the objective of maintaining your email inbox vacant) does not imply that you will never receive another email, adopting a zero harm culture entails taking each incident seriously and analyzing ways to prevent it from happening again.
There will still be risks and hazards, but a zero-harm firm is very well aware of them and has chosen to take every precaution to keep them from causing injury. If an incident occurs, it is investigated thoroughly and may result in the implementation of new policies and procedures.
Top Strategies for a Zero Harm Workplace
Creating safety policies and procedures that are robust
Do you know what is your biggest asset and what it can do?
It’s your workforce that can prevent or cause an accident in the workplace.
To advertise a zero-harm culture of safety and consciousness, your employees must be aware of your workplace expectations, including adherence to best practice safety culture.
It is one thing to have well-designed safety processes, but it is quite another to ensure that they are effectively communicated.
Often, an employee will be given an introduction to OH&S during their induction and then on an annual basis after that.
Although classical, this is far from an effective method of accident prevention planning when these are processes that must be remembered every day to be effectively implemented.
Safety officers and managers should develop strong safety rules and regulations that are clearly provided to employees. It is, without a doubt, a traditional approach to improving workplace safety, but it consistently helps reduce incidents.
Ideally, your company will develop enhanced safety procedures after deciding to truly accept the zero-harm culture. Employees should be thoroughly trained on your new policies.
Risk Management
Every facility manager is familiar with the key steps of risk management, which include identifying dangers, evaluating risks, managing risks, and reviewing control measures. These steps have become an acquainted safety mantra, repeated from within by facility managers all over the world to reduce the risk and occurrence of employee injuries. Familiarity, on the other hand, breeds complacency, so it is vital to maintain that risk management is integrated into every staff person's daily routine.
Creating a zero-harm culture in which every task performed is naturally linked to an awareness of the risks associated with that task is critical for helping to manage risk in the workplace.
Reporting Systems
How does your organization keep track of safety inspections? If you still use paper checklists, you're missing out on managers' ability to track and supervise safety checks for the entire company.
A comprehensive inspection software solution enables your employees to thoroughly document a report on safety audits as they go about their daily tasks. This strategy is critical for fully embracing the zero harm culture because it significantly improves the clarity and accountability of safety inspections.
Inspection software digitizes this vital information, which can then be used to inform data-driven decisions that make third-party audits much easier.
These strategies will improve the workplace and prevent any incidents from happening. As told above, you cannot avoid an incident, but you can delay the chances of it occurring again and again.
On the World Day for Safety and Health at Work, we will tell you a few ways that can help you in improving safety and health at the workplace. Let’s talk about it:
- Train your employees well
- If an employee shows safe behavior, reward him.
- Have a partnership with some occupational clinicians
- Use signs and labels for easy communication
- Maintain sanitary conditions around the office.
- Supply the right tools to your employees and plan routine equipment inspections.
- Encourage much-needed stretch breaks
- Implement every safety protocol from the start
- Keep an open dialogue with your employees
- Conduct regular meetings on workplace safety.
These are some of the improvement points that will make your workplace a zero-harm zone and increase productivity. As a reader, it is your decision to apply these bullet points and see the changes. If your employees are safe and sound, they will work harder and will benefit your organization.
We wish you a World Day of Safety and Health, and we hope you will make your workplace a better place to work at.
You May Like
EDITOR’S CHOICE