Optimizing 3D Printing Speed – Tips and Tricks for Maximum Efficiency
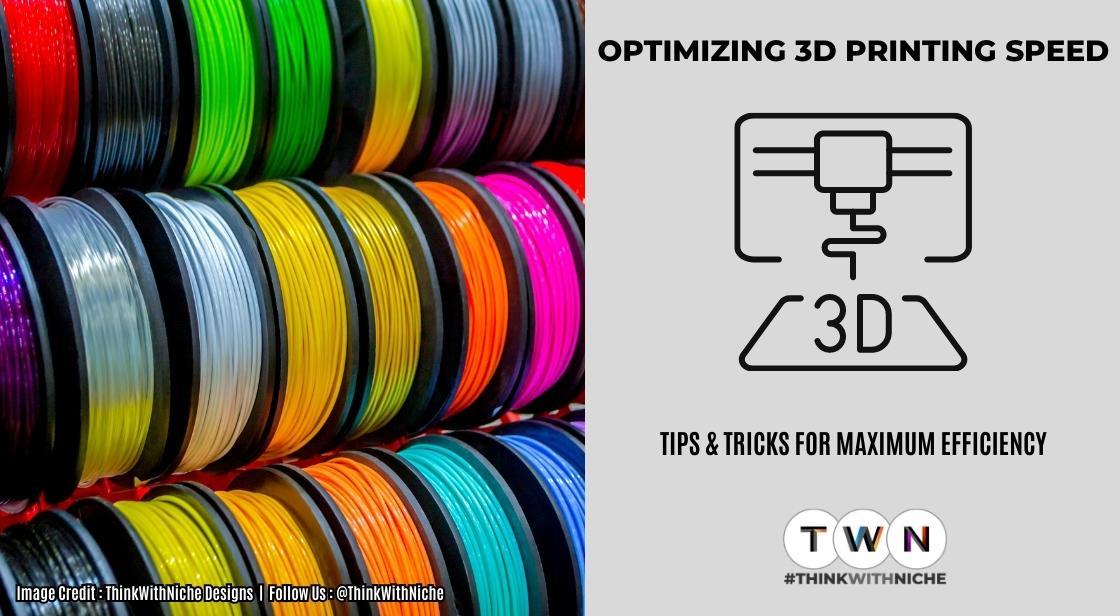
Blog Post
3D printing has revolutionized the manufacturing industry, but printing speed can often be a limiting factor. By optimizing printing speed, manufacturers can improve efficiency and reduce production costs. In this article, we will provide tips and tricks for maximizing 3D printing speed while maintaining print quality.
layer height is the thickness of each layer of material that is deposited during the printing process. By reducing the layer height, manufacturers can print parts more quickly, as each layer will be thinner and require less time to print. However, reducing the layer height too much can result in a decrease in print quality, so it is important to find the right balance between speed and quality.
There may be times when you want to speed up your 3D printing experience – but without risking the quality of your prints. Fortunately, there are a number of hardware and software adjustments you can make to achieve this.
The right setting can strike the perfect balance between quality, accuracy, and strength. It's also a good idea to experiment with different settings until you find what works best for your printer and material.
Optimizing 3D Printing Speed – Tips and Tricks for Maximum Efficiency
Preparing for Maximum Efficiency
Whether you are a small business owner or an industry expert, optimizing your 3D printing speed can help you increase productivity and lower costs. Unless you have some of the fastest 3D printers nowadays, by applying these tips and tricks, you can optimize the printing process, reduce downtime, and improve the quality of your products.
-
Prepare your CAD model correctly. This means creating a model that has the right layer height and infill density settings. This will allow your printer to create stronger and more solid parts that are less likely to break during production.
-
Set your part orientation. This can impact the strength of your part, the amount of time it takes to print, and the surface quality of your model. It is recommended that you design your parts with this setting in mind during the slicing process.
-
Adjust your infill density and wall thickness to ensure that your 3D printed part is strong enough for the task at hand. However, be careful not to overdo it; you want to maintain a consistent strength throughout your prints.
One of the best ways to ensure that your parts are strong is to design them such that the largest forces will traverse planes parallel to the print bed. This will allow for increased durability and strength, especially if you are using continuous fiber to reinforce the part.
Utilizing Advanced Settings
Utilize advanced settings to improve speed and quality without compromising the end product. These adjustments can help you save time, increase productivity, and reduce the overall costs of printing.
-
Change the layer height. Higher layer heights can help you produce thicker layers, which in turn, will result in a shorter print time. However, this can come at the cost of decreased detail.
-
Adjusting to maximize your 3D printer’s potential is infill density. This setting can help you reduce the amount of infill used at the bottom of your models, and instead use it at the top.
-
Using gradient infill steps is also a great way to optimize the amount of infill that is used during your prints. This allows you to halve the amount of infill used at each level, which can significantly increase your print speed.
-
Adjust the number of shells and perimeters that you use when printing your 3D model. These are important settings to remember if you are printing small or delicate parts that require strength. Decreasing the numbers for these settings can help you speed up your prints while still preserving the structural capabilities of your 3D models.
Selecting the Right Print Quality
The first step in determining the right print quality is understanding how it relates to your project. Depending on your goals, certain prints may require higher layer heights for better quality and/or speed.
Thinner layers result in more detail and a smoother surface, but they also take longer to print.
If you’re printing a prototype or functional print that doesn’t need to be as detailed, then using finer layer heights can save time and improve quality. However, if you’re trying to print a final product for display, then you’ll want to use the highest quality possible for optimal results.
Consider nozzle size. A larger nozzle will increase your printing speeds, but can also cause a significant decrease in print quality.
Optimizing Movement Speeds
When printing 3D models, it is important to optimize movement speeds. This will help you save time while still maintaining a high level of quality.
There are several factors that affect movement speed, such as the strength of a structure and the amount of detail in its design. Moreover, the size of an object also has an impact on its print speed.
The efficiency of a print can be influenced by infill density. Generally speaking, larger objects require more infill to maintain their shape, while smaller ones need less infill to achieve their intended shape.
The type of materials used in a print can also have an effect on the printer's overall performance. For example, flexible filaments like TPU require slower print speeds than rigid ones, such as PLA and ABS.
Likewise, the complexity of the geometry that the 3D printer has to work with can also impact its printing speed. An intricate part that requires lots of non-extrusion movements, bends, and turns will take longer to print than a linear part that has simpler geometrical shapes.
A third way to increase the printer's speed is to adjust its acceleration and jerk values. These parameters control the intensity of movement on both axes, and you can set them in most slicers.
Also Read: Why Cloud Web Security Is More Important Than Ever in a Post-Pandemic World
Monitoring Print Progress and Making Adjustments
Scientists and engineers are constantly developing new materials with unique properties that make them ideal for 3D printing. But figuring out how to print these materials effectively can be a complex and costly process. Expert operators often must manually trial-and-error – potentially making thousands of prints – to determine the best printing parameters for each new material.
MIT researchers have now used artificial intelligence to streamline this procedure. They developed a machine-learning system that uses computer vision to watch the manufacturing process and then correct errors in how it handles the material in real time.
The system can also be adjusted on-the-fly, so engineers can make adjustments on the fly to handle unexpected changes in material or environment conditions. They are already using it to produce a 3D medical model that doctors can use for pre-operative planning and surgical preparation. The researchers hope to develop controllers for other manufacturing processes, too.
Final Words
By optimizing 3D printing speed, users can experience a range of benefits. This includes faster production times, improved print quality and reduced material waste. With some trial and error, experimentation with settings and patience, users can make their 3D printing process more efficient and cost-effective. With the right setup, 3D printing can be a time-saving and enjoyable experience.
You May Like
EDITOR’S CHOICE