Value Chain vs. Supply Chain: What's the Difference?
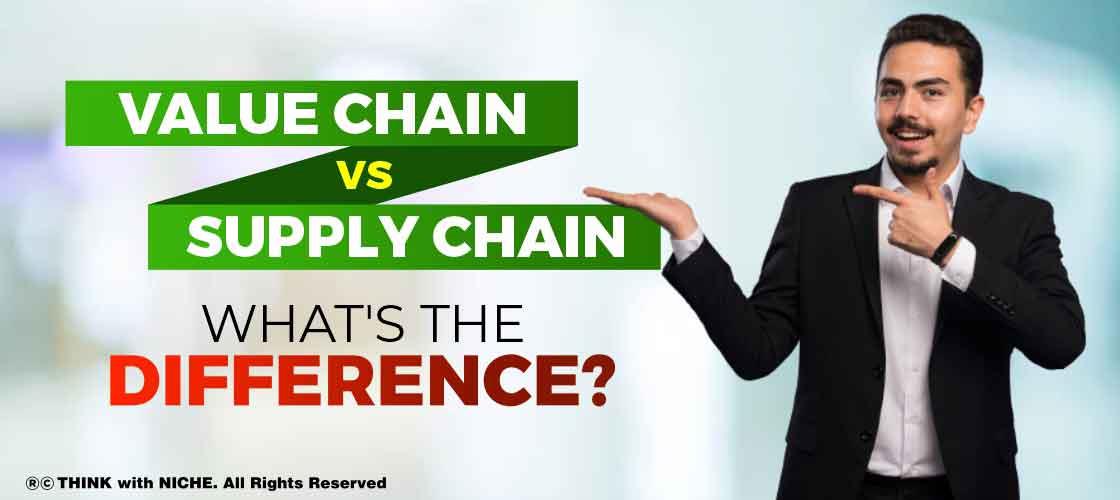
Blog Post
A company's value chain is the process through which it adds value to its raw materials to manufacture products that are finally sold to consumers. The supply chain encompasses all of the procedures involved in getting a product to a customer.
The process by which businesses receive raw materials, add value to them through production, manufacturing, and other processes to create a finished product, and then sell the final product to customers is referred to as the value chain. A supply chain reflects the procedures used to bring a product or service to a client, which frequently involves Original and aftermarket parts.
A value chain is a collection of interconnected activities that a corporation utilizes to establish a competitive advantage, whereas a supply chain involves all parties in fulfilling a customer request and resulting in consumer satisfaction. In this blog post, we will explore the distinctions between the Value Chain and the Supply Chain.
The term "value chain" refers to the process by which firms take raw materials, add value to them through production, manufacturing, and other processes to create a finished product, and then sell that product to consumers. The stages involved in getting a product or service to a consumer are called a supply chain, and they frequently involve OEM and aftermarket parts. A value chain is a collection of interconnected activities that a company uses to gain a competitive advantage. While a supply chain involves all parties in fulfilling a customer request and leading to customer satisfaction, a supply chain is a collection of interconnected activities that a company uses to gain a competitive advantage.
Value Chain vs. Supply Chain: What's the Difference?
Value Chain
In his 1985 book Competitive Advantage: Creating and Sustaining Superior Performance, American academic Michael Porter popularized the concept of a value chain. He utilized the concept to demonstrate how businesses add value to their basic resources to create products that are then sold to the general population. The value chain is a concept that comes from the world of business management. Value chain managers seek ways to improve the company's bottom line. They might seek ways to reduce shortages, make product strategies, and collaborate with others in the supply chain to provide more value to the client. The value chain is made up of five steps. They enable a company to create value that is greater than the cost of providing goods or services to customers. A corporation can get a competitive edge over competitors in its industry by maximizing the activity in any of the five steps. The following are the five steps or activities:
Customer support and warranty service are examples of service activities that sustain and enhance the value of a product. Porter claims that the value chain requires a range of support operations to assist streamline the five core processes. Procurement, technological development, human resource management, and infrastructure are just a few examples.
Also Read: What are the Primary Activities of Michael Porter's Value Chain?
The value chain process has five stages. They allow a company to generate value that exceeds the cost of supplying goods or services to consumers. Increasing activity in any of the five processes gives a corporation a competitive advantage over competitors in its industry. The five steps or activities are as follows:
Five stages of the value chain process
1. Inbound Logistics: Receiving, warehousing, and inventory control are all examples of inbound logistics.
2. Operations: Value-creating operations such as assembly and manufacturing that turn inputs into products.
3. Outbound Logistics: The activities necessary to deliver a finished product to a client. Warehousing, inventory management, order fulfillment, and shipping are some examples.
4. Marketing and Sales: Marketing and sales are the activities involved in convincing a buyer to buy a product.
5. Service: Customer assistance and warranty service are examples of service activities that sustain and increase the value of a product.
Definition of Value Chain
The value chain is the set of activities that add value at every stage of creating, manufacturing, and delivering a high-quality product to the client. Value Chain Analysis is used to examine actions within and outside the business that are related to the firm's capacity to give value for money, commodities, and services.
Michael Porter developed the idea of Value Chain Analysis in his acclaimed book "Competitive Advantage" in 1985. Two key phases in the value chain analysis, in his perspective, are:
- Individual activity identification
- Assessing the value added in each activity and linking it to the firm's competitiveness.
Supply Chain
The supply chain refers to the flow of all data, products, materials, and cash between the many stages of developing and selling a product to the ultimate user. From the standpoint of operational management, the supply chain is a notion. A company's supply chain encompasses every step of the process, including designing a product or service, manufacturing it, transporting it to a point of sale, and selling it. All functions involved in receiving and fulfilling a client's request are included in the supply chain. These are some of the functions:
- Product development
- Marketing
- Operations
- Distribution
- Finance
- Customer service.
At large corporations, supply chain management is a critical operation that involves many interconnections. As a result, supply chain management necessitates a high level of expertise and talent to sustain.
The Definition of Supply Chain
The supply chain connects all of the persons, resources, enterprises, and activities involved in the marketing or distribution of a product to the ultimate consumer. It connects channel partners such as suppliers, manufacturers, wholesalers, distributors, retailers, and customers. Simply expressed, it is the movement and storage of raw materials, semi-finished items, and completed commodities from their point of origin to their eventual destination, i.e. consumption.
Supply Chain Management refers to the practice of planning and controlling supply chain activities. It is a cross-functional system that handles the flow of raw materials inside the organization as well as the movement of completed items out of the company, all while providing complete customer satisfaction. The supply chain includes the following activities:
- Integration
- Sharing of Information
- Development of product
- Procurement
- Production
- Distribution
- Services to customer
- Performance analysis
Also Read: What Are the Effects of Backward Integration?
Differences Between the Supply Chain and the Value Chain
The primary distinctions between supply chain and value chain are as follows:
- The supply chain is the integration of all the activities, people, and businesses that move a product from one location to another. A value chain is a series of activities that add value to a product at every stage until it reaches the end customer.
- The Supply Chain notion evolved from operational management, whereas the Value Chain concept evolved from business management.
- The movement of materials from one location to another is one of the Supply Chain operations. The value Chain, on the other hand, is primarily concerned with offering a good or service for a reasonable price.
- The supply chain order begins with the product request and concludes when it reaches the client. In contrast to the value chain, which starts with the customer's request and finishes with the product.
- The primary goal of the supply chain is to achieve 100% customer satisfaction, which is not the case with the Value Chain.
Conclusion
While many people associate logistics—or the transportation of goods—with the supply chain, it is simply one aspect of the process. The supply chain is responsible for coordinating how and when things are created, as well as how they are delivered. The cost of materials and effective product delivery are the two main objectives of supply chain management. Proper supply chain management can lower consumer costs while increasing company profitability.
You May Like
EDITOR’S CHOICE